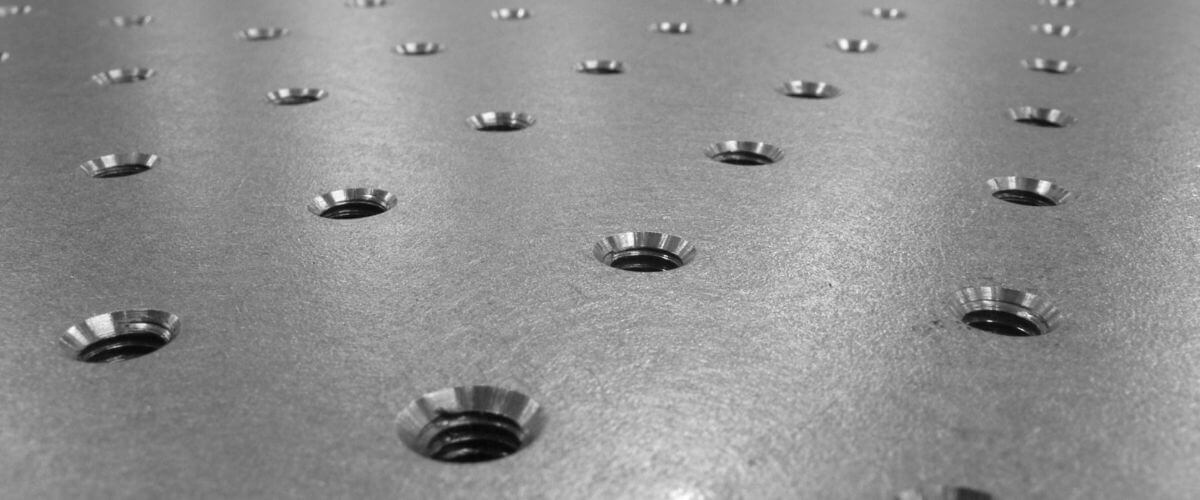
Optical engineers performing tests and manufacturing optical components and equipment require a stable work surface possessing specific vibration dampening qualities that help to keep carefully calibrated equipment from being shifted. Optical engineering is a technical, highly precise field, one that often takes place on a microscopic scale.
Pieces and components must be precisely placed, and the slightest deviation from these careful measurements can ruin an experiment or render a piece of equipment useless.
In some cases, engineers may use an optical table, a heavy-duty four-legged work table designed to absorb, isolate, and dampen vibrations created by the surrounding environment or by equipment atop the table. Optical breadboards are a portable, smaller version of optical tables, which can be used in conjunction with optical tables or used as a suitable replacement where an optical table may be impractical.
Optical Breadboard Overview
Optical breadboards are legless platforms made from solid aluminum, carbon, or steel. The top surface of an optical breadboard features a grid of evenly spaced threaded holes to accommodate mounted equipment and optical components.
These holes are typically spaced between ½ an inch and one inch apart and can accommodate standard ¼ inch screws. Each hole is closed at the bottom to contain small pieces.
The internal body of an optical breadboard is comprised of a honeycomb lattice structure, similar to the inner structure of a standard optical table, though not all optical breadboards include this additional body. Thicker breadboards may be equipped with additional dampening features such as insulating fillers, while others may rely solely on rigidity to reduce vibrations.
To provide additional vibration isolation and dampening to thinner optical breadboards, some technicians may place these platforms atop soft air springs or other shock-absorbing accessories.
Qualities of Optical Breadboards
Acoustic breadboards are extremely rigid and inflexible, not bending or flexing under changing loads or amid experimentation. Lightweight enough to accommodate travel, or to be moved to different areas of a facility without much effort.
Some breadboards are designed to be affixed above standard optical tables to provide additional height or extra surface area, whereas others are designed for optimum portability.
Applications of Optical Breadboards
While optical tables are standard in many optical engineering and manufacturing facilities, there are occasions when a smaller, portable option is needed. Here are just a few common applications of breadboards:
- Used With Optical Tables: Some engineers like to affix optical breadboards to the tops of their optical tables, creating a solid, unyielding, entirely level surface on which to work. Once a task is complete, the breadboard can be removed from the table, creating space for a new task without needing to disassemble the components already attached to the breadboard. This function allows researchers and technicians to work on multiple projects at once, or move projects to various locations without destroying the work they have already done.
- Travel: Optical engineers work in a variety of conditions, and may need a sturdy, completely flat surface in a pinch. An optical breadboard can easily be taken along on travels to be used on the road, or as an optical table replacement in a non-permanent location. For example for demonstrations or visiting engineers.
- Education: Because optical breadboards are portable, they make excellent educational tools. Educational lab environments have frequent turnovers of students, often need to be cleaned, and are used for a wide range of purposes. As such, many labs don’t have the space for full-sized optical tables, and instead mount breadboards on regular worksurfaces to create an excellent alternative for student learning.
Optical Tables vs. Breadboards
Often used interchangeably, optical breadboards and optical tables possess many of the same qualities, but that doesn’t mean that they are the same. Depending on your specific needs, an optical table may be more useful than an optical breadboard, or vice versa. Here are a few of the key differences between the two:
- Vibration Dampening: While an optical breadboard can help create a flat surface on which to work, and may absorb some vibration, optical tables provide far greater vibration dampening power. If your working environment is high-vibration, an optical table is the better option.
- Flexibility: No, we don’t mean literal flexibility, since both of these tools provide intense rigidity to prevent flexing and accidental movement – but if you need to be able to move experiments or projects around, you’ll want to select a breadboard. Breadboards can be affixed to virtually any surface, can easily be moved to new locations, and are even easy to travel with.
- Stability: One of the reasons optical engineers use optical tables and breadboards is to stabilize devices, components, and various projects. Careful alignment is often required for experiments or devices to work, which means that items must stay firmly in one place once calibrated. While breadboards can provide a solid surface on which to build or affix components, they may not provide the same unmoving stability as an optical table, since optical breadboards are inherently designed for a certain amount of portability.
Need More Information on Industrial Furniture Options For Your Lab?
Visit OnePointe Solutions online today to browse our selection of quality lab furniture, and be sure to check out our blog for more information on topics like this and much more.